焊接机器人控制系统有哪些,焊接机器人控制系统【最新推荐】
焊接机器人控制系统有哪些,焊接机器人在现代制造业中扮演着越来越重要的角色,其高效、精准、稳定的焊接性能极大地提升了生产效率和产品质量。而焊接机器人的核心——控制系统,更是决定了其性能的优劣。本文将详细介绍焊接机器人控制系统的主要类型、功能与特点,帮助读者更好地了解这一关键技术。接下来就和锦科绿色小编一起来看看吧。
一、焊接机器人控制系统的主要类型
(一)可编程逻辑控制器(PLC)控制系统
PLC控制系统是早期焊接机器人中常见的控制方式之一。它通过预先编写的程序,控制焊接机器人的动作序列和焊接参数。PLC具有较高的可靠性和稳定性,适用于焊接任务相对固定、工艺流程较为简单的应用场景。其主要功能包括:
动作控制:根据预设程序,精确控制焊接机器人的运动轨迹和速度。
焊接参数设置:调节焊接电流、电压、送丝速度等参数,确保焊接质量。
故障诊断与报警:实时监测系统状态,一旦出现异常,及时发出警报并停机,保障设备安全。
然而,PLC系统的灵活性相对较差,难以适应复杂的焊接任务和频繁的工艺变更。
(二)专用焊接机器人控制系统
随着焊接机器人技术的发展,越来越多的机器人制造商开发了专用的控制系统。这些系统专为焊接机器人设计,集成了先进的运动控制算法、焊接工艺数据库和人机交互界面,具有以下特点:
高度集成化:将机器人运动控制、焊接参数管理、传感器信号处理等功能集成于一体,简化了系统架构,提高了运行效率。
智能焊接功能:内置多种焊接工艺程序,能够根据不同的焊接材料、接头形式和焊接要求,自动调整焊接参数,实现智能化焊接。
离线编程与仿真:支持离线编程功能,用户可以在计算机上进行焊接程序的编写和仿真调试,无需占用机器人实际运行时间,大大提高了生产效率和程序的准确性。
实时监控与数据分析:通过网络接口与上位机连接,实现对焊接过程的实时监控和数据采集,便于质量追溯和工艺优化。
专用焊接机器人控制系统在汽车制造、航空航天、机械加工等复杂焊接领域得到了广泛应用。
(三)基于PC的开放式控制系统
近年来,随着计算机技术的飞速发展,基于PC的开放式控制系统逐渐应用于焊接机器人领域。这种系统以工业PC为核心,结合先进的运动控制卡和软件平台,具有以下优势:
开放性与可扩展性:基于PC的架构使得系统具有良好的开放性和可扩展性,用户可以根据需要方便地添加功能模块,如视觉系统、传感器接口等,以满足不断变化的焊接需求。
强大的计算能力:利用PC的高性能处理器,能够实现复杂的运动规划、路径优化和多任务处理,支持高级的焊接工艺算法,如自适应焊接控制、智能轨迹规划等。
友好的人机交互界面:借助成熟的软件开发工具,可以设计出直观、易用的人机交互界面,方便操作人员进行程序编写、参数设置和运行监控。
与企业信息化系统的集成:易于与企业的MES(制造执行系统)、ERP(企业资源计划)等信息化系统进行无缝集成,实现生产过程的自动化管理和信息化追溯。
基于PC的开放式控制系统为焊接机器人提供了更广阔的发展空间,尤其适合对焊接质量和生产管理要求较高的高端制造领域。
二、焊接机器人控制系统的关键功能模块
(一)运动控制模块
运动控制是焊接机器人控制系统的核心功能之一。它负责根据焊接任务的要求,精确地控制机器人的关节运动,生成所需的焊接轨迹。主要功能包括:
路径规划:根据焊接模型和工艺要求,计算机器人从起始点到终点的最优运动路径,避免碰撞和奇异点。
速度与加速度控制:精确控制机器人的运动速度和加速度,确保焊接过程的平稳性和焊接质量的稳定性。
多轴协调运动:实现多个关节的同步协调运动,保证焊接工具在空间中的精确姿态和位置控制。
(二)焊接参数控制模块
焊接参数的精确控制直接影响焊接质量和效率。该模块的主要功能包括:
参数设置与调整:允许用户根据焊接材料、厚度和工艺要求,设置焊接电流、电压、送丝速度、焊接速度等参数。
实时监测与反馈:实时监测焊接过程中的参数变化,并根据反馈信号自动调整参数,以适应焊接条件的变化,实现自适应焊接控制。
工艺数据库管理:存储多种焊接工艺参数组合,用户可以根据不同的焊接任务快速调用相应的工艺参数,提高生产效率和焊接质量的一致性。
(三)传感器信号处理模块
为了实现智能化焊接,焊接机器人通常配备多种传感器,如视觉传感器、激光传感器、电弧传感器等。传感器信号处理模块负责对这些传感器采集的数据进行处理和分析,为机器人的运动控制和焊接参数调整提供依据。其功能包括:
信号采集与预处理:对传感器信号进行采集、滤波、放大等预处理操作,提高信号的质量和可靠性。
数据融合与分析:将来自不同传感器的数据进行融合分析,提取有用的信息,如焊缝位置、形状、熔池状态等。
反馈控制:根据传感器数据的分析结果,实时调整机器人的运动轨迹和焊接参数,实现焊接过程的智能化控制。
(四)人机交互模块
人机交互模块是操作人员与焊接机器人控制系统之间沟通的桥梁。其主要功能包括:
程序编写与调试:提供直观的编程界面,支持图形化编程、离线编程等多种编程方式,方便操作人员编写和调试焊接程序。
参数设置与调整:允许用户通过操作界面方便地设置和调整焊接参数、运动参数等系统参数。
运行监控与故障诊断:实时显示焊接机器人的运行状态、焊接参数、报警信息等,帮助操作人员及时发现和处理问题,确保焊接过程的顺利进行。
数据记录与追溯:记录焊接过程中的关键数据,便于质量追溯和工艺优化。
(五)网络通信模块
随着工业自动化和信息化的发展,焊接机器人控制系统需要与其他设备和系统进行通信和协同工作。网络通信模块的主要功能包括:
与上位机通信:通过以太网、串口等通信接口与企业的MES、ERP等上位机系统进行数据交互,实现生产任务的分配、焊接数据的上传和生产过程的监控。
与外部设备通信:与焊接电源、变位机、上下料装置等外部设备进行通信和协同控制,实现焊接生产线的自动化和智能化。
远程监控与诊断:支持通过网络进行远程监控和诊断,技术人员可以通过远程终端实时查看焊接机器人的运行状态,进行故障诊断和程序调整,提高设备的维护效率和可用性。
锦科绿色科技(苏州)有限公司对设备软硬件的研发设计,制造生产、有其丰富的实战成绩,以非标自动化,环境自动化为工程主项目,以沸石转轮和软件控制为产品核心。产品涉及生态环境的水体,土壤,空气的监测与治理修复,构建智能生物生态链,工业生产环境中的智能制造,办公环境中云系统服务三大领域。
综上所述,焊接机器人控制系统是焊接机器人实现高效、精准焊接的关键技术。从早期的PLC控制系统到专用焊接机器人控制系统,再到基于PC的开放式控制系统,其功能和性能不断提升,为现代制造业的发展提供了强大支持。感谢阅读,想了解更多欢迎继续阅读《焊接机器人有哪些应用,焊接机器人应用领域》。
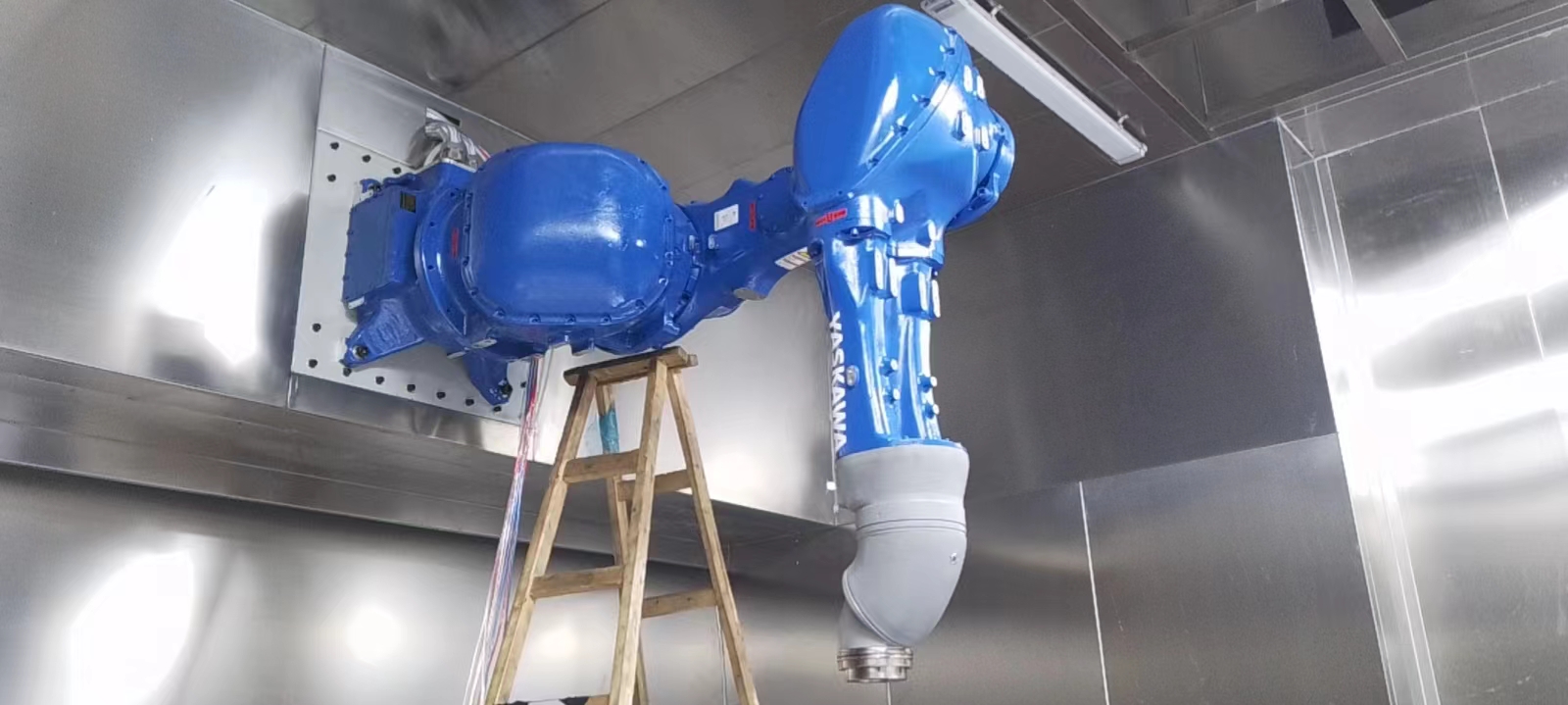
(一)可编程逻辑控制器(PLC)控制系统
PLC控制系统是早期焊接机器人中常见的控制方式之一。它通过预先编写的程序,控制焊接机器人的动作序列和焊接参数。PLC具有较高的可靠性和稳定性,适用于焊接任务相对固定、工艺流程较为简单的应用场景。其主要功能包括:
动作控制:根据预设程序,精确控制焊接机器人的运动轨迹和速度。
焊接参数设置:调节焊接电流、电压、送丝速度等参数,确保焊接质量。
故障诊断与报警:实时监测系统状态,一旦出现异常,及时发出警报并停机,保障设备安全。
然而,PLC系统的灵活性相对较差,难以适应复杂的焊接任务和频繁的工艺变更。
(二)专用焊接机器人控制系统
随着焊接机器人技术的发展,越来越多的机器人制造商开发了专用的控制系统。这些系统专为焊接机器人设计,集成了先进的运动控制算法、焊接工艺数据库和人机交互界面,具有以下特点:
高度集成化:将机器人运动控制、焊接参数管理、传感器信号处理等功能集成于一体,简化了系统架构,提高了运行效率。
智能焊接功能:内置多种焊接工艺程序,能够根据不同的焊接材料、接头形式和焊接要求,自动调整焊接参数,实现智能化焊接。
离线编程与仿真:支持离线编程功能,用户可以在计算机上进行焊接程序的编写和仿真调试,无需占用机器人实际运行时间,大大提高了生产效率和程序的准确性。
实时监控与数据分析:通过网络接口与上位机连接,实现对焊接过程的实时监控和数据采集,便于质量追溯和工艺优化。
专用焊接机器人控制系统在汽车制造、航空航天、机械加工等复杂焊接领域得到了广泛应用。
(三)基于PC的开放式控制系统
近年来,随着计算机技术的飞速发展,基于PC的开放式控制系统逐渐应用于焊接机器人领域。这种系统以工业PC为核心,结合先进的运动控制卡和软件平台,具有以下优势:
开放性与可扩展性:基于PC的架构使得系统具有良好的开放性和可扩展性,用户可以根据需要方便地添加功能模块,如视觉系统、传感器接口等,以满足不断变化的焊接需求。
强大的计算能力:利用PC的高性能处理器,能够实现复杂的运动规划、路径优化和多任务处理,支持高级的焊接工艺算法,如自适应焊接控制、智能轨迹规划等。
友好的人机交互界面:借助成熟的软件开发工具,可以设计出直观、易用的人机交互界面,方便操作人员进行程序编写、参数设置和运行监控。
与企业信息化系统的集成:易于与企业的MES(制造执行系统)、ERP(企业资源计划)等信息化系统进行无缝集成,实现生产过程的自动化管理和信息化追溯。
基于PC的开放式控制系统为焊接机器人提供了更广阔的发展空间,尤其适合对焊接质量和生产管理要求较高的高端制造领域。
二、焊接机器人控制系统的关键功能模块
(一)运动控制模块
运动控制是焊接机器人控制系统的核心功能之一。它负责根据焊接任务的要求,精确地控制机器人的关节运动,生成所需的焊接轨迹。主要功能包括:
路径规划:根据焊接模型和工艺要求,计算机器人从起始点到终点的最优运动路径,避免碰撞和奇异点。
速度与加速度控制:精确控制机器人的运动速度和加速度,确保焊接过程的平稳性和焊接质量的稳定性。
多轴协调运动:实现多个关节的同步协调运动,保证焊接工具在空间中的精确姿态和位置控制。
(二)焊接参数控制模块
焊接参数的精确控制直接影响焊接质量和效率。该模块的主要功能包括:
参数设置与调整:允许用户根据焊接材料、厚度和工艺要求,设置焊接电流、电压、送丝速度、焊接速度等参数。
实时监测与反馈:实时监测焊接过程中的参数变化,并根据反馈信号自动调整参数,以适应焊接条件的变化,实现自适应焊接控制。
工艺数据库管理:存储多种焊接工艺参数组合,用户可以根据不同的焊接任务快速调用相应的工艺参数,提高生产效率和焊接质量的一致性。
(三)传感器信号处理模块
为了实现智能化焊接,焊接机器人通常配备多种传感器,如视觉传感器、激光传感器、电弧传感器等。传感器信号处理模块负责对这些传感器采集的数据进行处理和分析,为机器人的运动控制和焊接参数调整提供依据。其功能包括:
信号采集与预处理:对传感器信号进行采集、滤波、放大等预处理操作,提高信号的质量和可靠性。
数据融合与分析:将来自不同传感器的数据进行融合分析,提取有用的信息,如焊缝位置、形状、熔池状态等。
反馈控制:根据传感器数据的分析结果,实时调整机器人的运动轨迹和焊接参数,实现焊接过程的智能化控制。
(四)人机交互模块
人机交互模块是操作人员与焊接机器人控制系统之间沟通的桥梁。其主要功能包括:
程序编写与调试:提供直观的编程界面,支持图形化编程、离线编程等多种编程方式,方便操作人员编写和调试焊接程序。
参数设置与调整:允许用户通过操作界面方便地设置和调整焊接参数、运动参数等系统参数。
运行监控与故障诊断:实时显示焊接机器人的运行状态、焊接参数、报警信息等,帮助操作人员及时发现和处理问题,确保焊接过程的顺利进行。
数据记录与追溯:记录焊接过程中的关键数据,便于质量追溯和工艺优化。
(五)网络通信模块
随着工业自动化和信息化的发展,焊接机器人控制系统需要与其他设备和系统进行通信和协同工作。网络通信模块的主要功能包括:
与上位机通信:通过以太网、串口等通信接口与企业的MES、ERP等上位机系统进行数据交互,实现生产任务的分配、焊接数据的上传和生产过程的监控。
与外部设备通信:与焊接电源、变位机、上下料装置等外部设备进行通信和协同控制,实现焊接生产线的自动化和智能化。
远程监控与诊断:支持通过网络进行远程监控和诊断,技术人员可以通过远程终端实时查看焊接机器人的运行状态,进行故障诊断和程序调整,提高设备的维护效率和可用性。
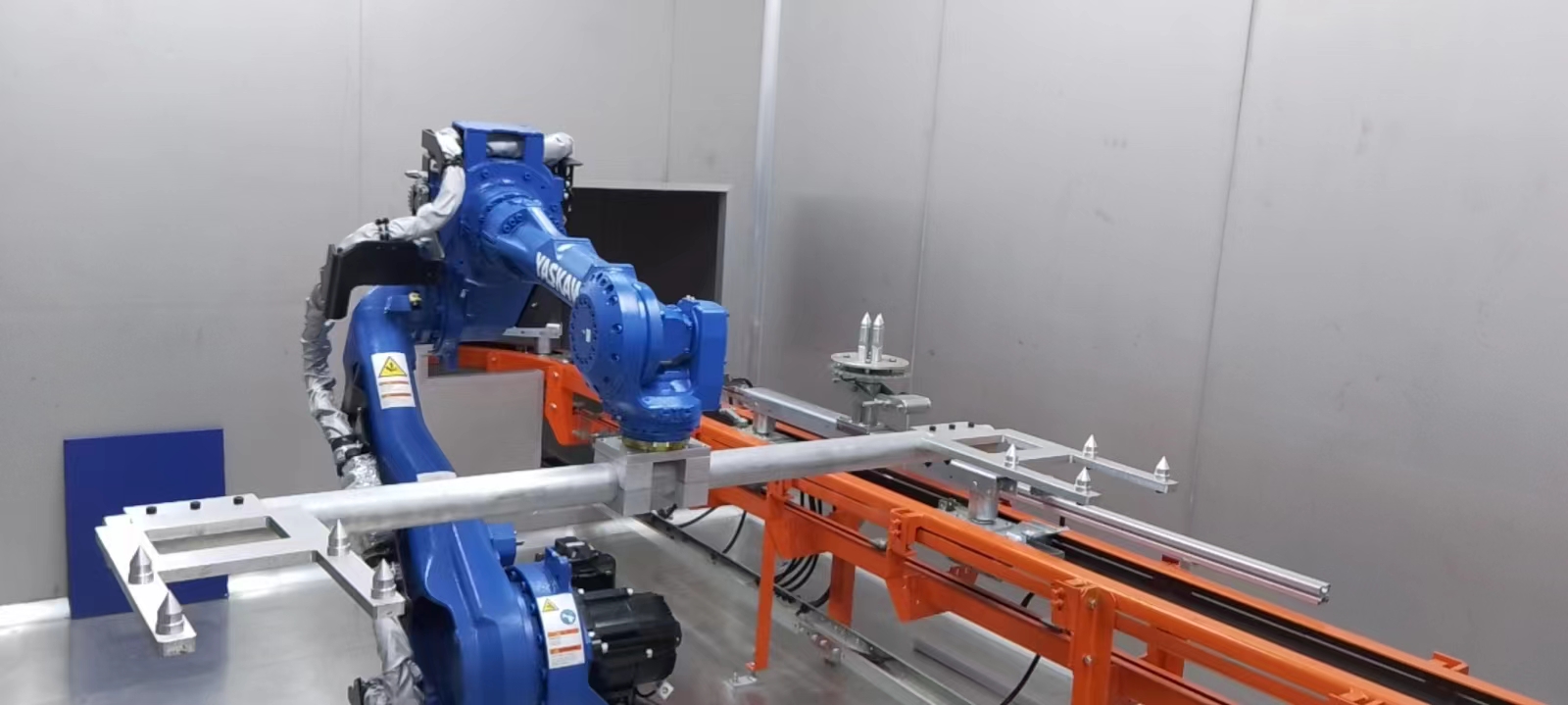
综上所述,焊接机器人控制系统是焊接机器人实现高效、精准焊接的关键技术。从早期的PLC控制系统到专用焊接机器人控制系统,再到基于PC的开放式控制系统,其功能和性能不断提升,为现代制造业的发展提供了强大支持。感谢阅读,想了解更多欢迎继续阅读《焊接机器人有哪些应用,焊接机器人应用领域》。